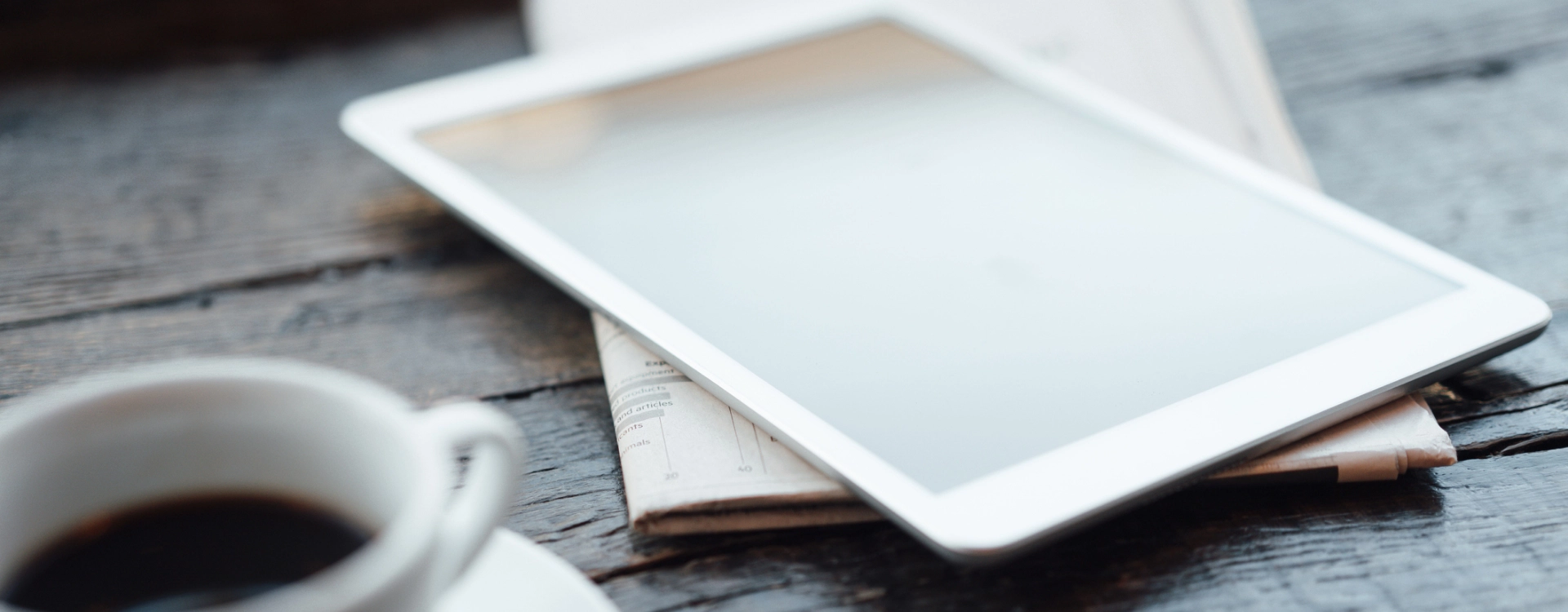
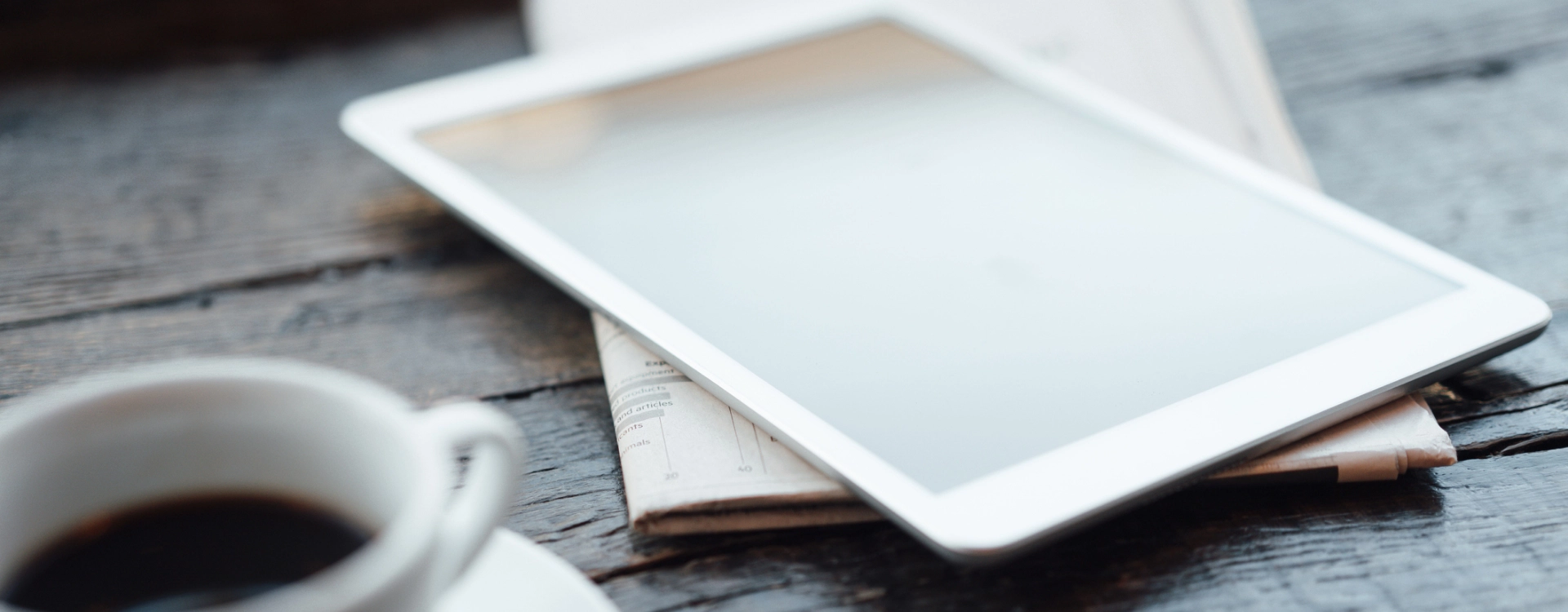
ENAXでは上記のような課題を解決するために、製品開発を目指すお客様の用途をヒアリングの上、課題を共有し、電極・電池の要素開発から試作および量産化までサポートしています。
具体的には、以下のような体制・プロセスに沿って研究開発を進めています。
1. 全個体電池に代表される次世代電池の概念実証
2. 製品搭載と同サイズの電池セルを用いた性能検証、生産課題の抽出
3. 量産プロセス設計と工程や品質の検証、QCの確立(組立における手順や工程の検討)
4. 数百~数万セルのプレ量産ニーズへの対応
5. パック組立プロセスの検証、部品変更の影響や作業安全性の検証
概念実証のラボスケールでの開発から製品実証としてパイロットスケールでのテスト・開発にも対応。パイロットスケールでの実証内容として、安全性や生産プロセスなどを評価することや、量産体制へ移管するにあたっての適性・妥当性を検証(バリデーション)することも大きなポイントとして挙げられます。
1.ご要望・開発要件
まずは電池に関するお困りごとや実現したいことをお伺いします。そのうえで、ENAXが製品実現に向けた電池の具体的な開発要件を定義します。
2.材料探索
リチウムイオン電池には正(負)極材や導電材、電解液、セパレーターといった様々な材料が用いられます。開発要件に応じて最適な材料を探索・選定します。
3.要素開発
要素開発とは、電極レシピや電解液のレシピ検討、その上で開発要件に応じた特性と合致しているかなどを確認するフェーズです。リチウムイオン電池の最小単位である単層パウチセルで行われます。
4.機能検証
製品搭載に向けた、実際のサイズに近しい積層セルにて検証が行われます例として製品に要求される入出力電流を印可した際の抵抗や発熱・耐久性・信頼性などを評価するフェーズです。
5.実機搭載検証
製品実装に必要なセル数から専用部材を必要量調達し、試作セルを量産に近しい設備・工程で製造するフェーズです。最終製品に搭載するセルとして各種性能が期待通りかの検証や法規制に対応するための試験などを行います。性能と品質に確認が取れ、小規模生産へ移管できるか判断するフェーズでもあります。
6.実機搭載品の小規模生産
量産工程へ移管するための準備にあたるフェーズです。主に量産数量を前提とした組み立て設備による製造プロセスやラインの調整、量産品質担保のための検査内容および検査工程調整、製造に伴う手順書やPL、QCなどの整備を行います。
7.量産移管
最終フェーズとして、量産体制へ移管します。量産数量によりますが、ENAXが量産を手掛けるだけではなく、お客様指定の製造先へ生産移管にもご対応いたします。
1.塗料化
電極を構成する活物質、助剤、バインダー、希釈液(水を含む両極性溶媒)を塗料にします。ENAXでは電池性能に寄与する塗料の分散性を中心に、配合レシピや作製プロセスの検証を行います。
2.塗工
塗料を集電箔にコーティングする工程です。ENAXでは高品質な塗工を実現するために、コンマリバースやコンマダイレクト、スロットダイの塗工方式を取り入れ、塗料物性の担保(※)と、バラつきを最小限に抑える塗工手法を確立します。塗料物性および塗工方法にムラやバラつきがあると、電池の出力や容量特性への不具合が出るだけでなく、発火などにつながる危険性もあります。また塗工工程の要素である電極乾燥は電池性能に直結するだけでなく、生産速度にも大きく関わるため、プロセス開発の要素として重視しています。
※塗料物性の担保=粘度変動の抑制・凝集物発生の抑制・塗工面安定の3要素を成立させること
3.プレス
塗工した電極の機械的強度を高めると同時に、活物質を集電体に密着させ、電気伝導を向上させるための工程です。電池の安定した入出力と容量・サイクル性能を担保するために、冷間および冷・熱間兼用のプレスを取り入れ、設計電極密度の達成、ならびに面内バラつきをコントロールします。
4.電極スリット
プレス電極を電池セルのサイズに合わせてスリット加工する工程です。ENAXではシャーカット方式に対応した機器によって、幅広いサイズの加工が可能です。
5.電池セル組立
一般的な電池セルの製造は以下の流れと環境下で行います。