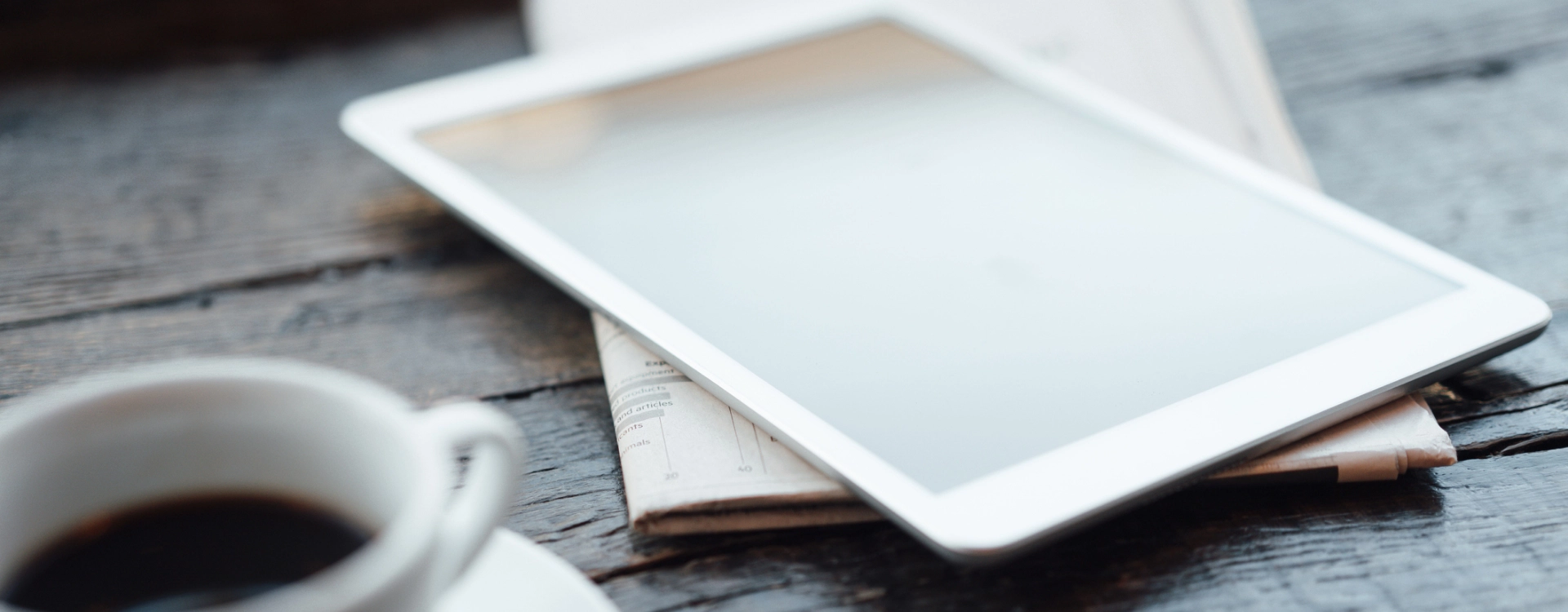
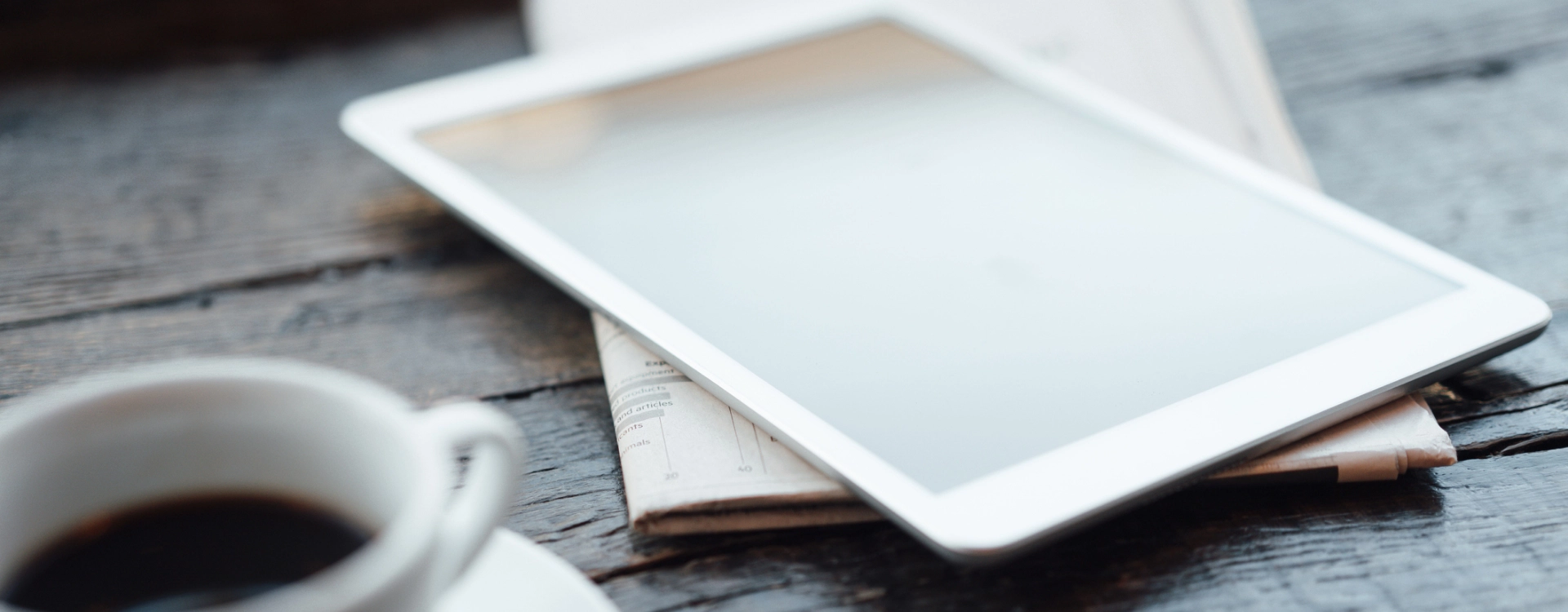
電池セルには様々な性能・規格のものがあります。用途に合わせて必要な性能が取り出せるよう、ENAXでは電池セルの選定および評価からモジュールの設計、電池パックユニットの構造設計を行っています。
構造設計で特に重要なのが、最初のステップである「企画」です。お客様からの要求事項や仕様などをヒアリングしたうえで、「目標とする性能」と「システムに適した形状」を両立するためのご提案をします。電池内部に使用する材料によっても最適な電池セルや筐体の形状は異なり、また納期や予算なども考慮しなければなりません。
ENAXでは電池開発の豊富なノウハウを活かし、どのような電池セルをいくつ採用し、容量や電圧の設定、指定された電流をクリアできるか、電池パックユニットとしての寿命が要望に応えられるかを判断したうえで、製品開発に取り組んでいます。
電池を搭載できるスペースの大きさや形状が決まっている状態で、問合わせがくるケースも少なくありません。その場合は、スペースや形状の制約をクリアする個別の筐体設計を行わなければなりません。お客様が求める仕様や性能の実現はもちろん、「電池のプロ」としてENAXが筐体設計に注力し、品質にこだわるポイントは以下の通りです。
1. 必要とされる電流容量を実現するバスバー設計および溶接技術
2. 電池の熱籠りおよび異常発生時の類焼を防止する熱設計
3. 電池の性能・寿命を引き出すための加圧拘束設計
4. 製品の機械的振動・衝撃に耐え得るモジュール固定設計
5. 局所・狭所に電力と信号を取りまわすための電線・FPC設計
特に熱設計やモジュール固定設計は安全に使用するためにも重要なプロセスであり、様々な試作や試験を繰り返しながら評価しています。
また、電池開発においては、「鉛電池に置き換えるだけ」といったイメージを持っている方も多く、開発費が発生することに驚かれるお客様も少なくありません。十分な品質要件の検討および設計を行わないまま商品開発を進めてしまうと、手戻りが発生し、それまでに費やされた時間や開発費用が無駄になってしまう恐れもあります。
このような事態を避けるために、ENAXでは原理試作から機能試作、量産前試作といった開発プロセスを経て量産体制へ移行します。
また、ENAXではお客様が実現したいことを企画段階からヒアリングし、既存製品・カスタムにかかわらず経済合理性の高いご提案を行います。
例えば、電池パックユニットの核となる電池セルは、コスト面や入手の容易さから中国製や韓国製、台湾製などの海外製品を使用することが少なくありません。海外製品に不安を持たれるかもしれませんが、充放電の制御や電池特性の確認、耐久性やライフサイクルの評価などを徹底して行い、安全性を担保しています。
釘刺し試験をはじめとした危険な破壊試験も、自社工場で実施。試験の様子と結果を動画で撮影し、お客様へ報告することも可能です。このように、安全面に配慮した製品開発を通じてバッテリーの内外で安全性を担保しています。