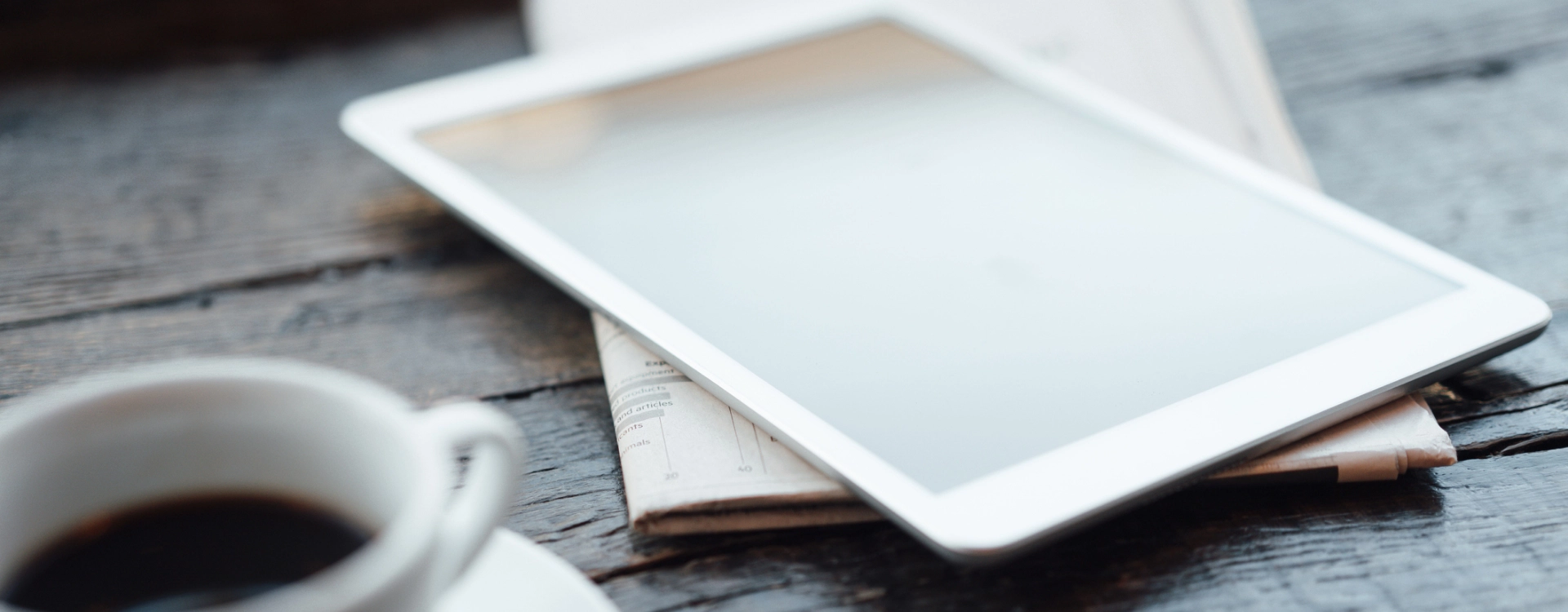
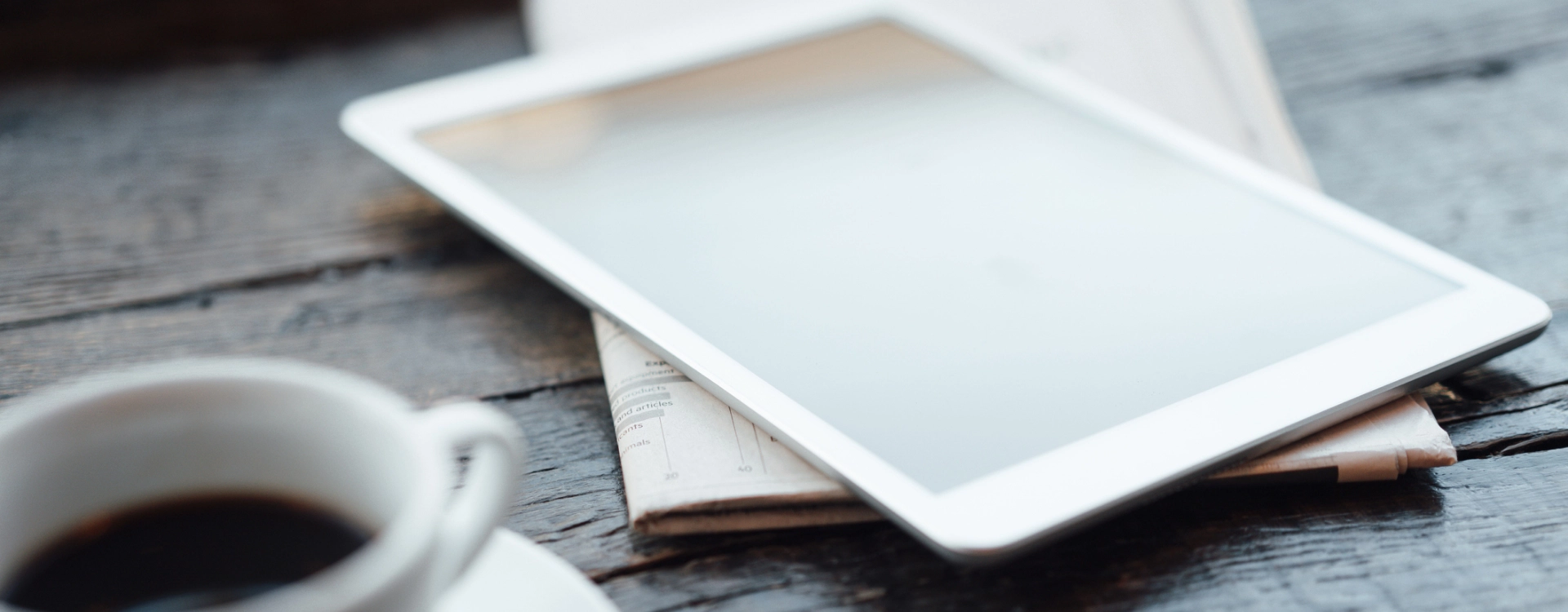
ENAX's contracted business to support R&D and mass production of next-generation batteries for a decarbonized society.
The need for the development of next-generation lithium-ion batteries is increasing due to the diversification of applications such as electric vehicles (EVs), small devices such as smartphones and tablet devices, and storage batteries for industrial and home use.
Since the development requirements for lithium-ion batteries vary depending on the application, ENAX is developing a battery development contract business that takes advantage of our specialized knowledge and technology. This page provides a detailed description of our R&D structure, development process, and processes.
While lithium-ion batteries have increased storage capacity and charging speed due to the diversification of their applications, they also pose risks that cannot be underestimated, such as heat generation, smoking, and ignition. Therefore, ensuring safety is an important issue in both R&D, quality assurance, and quality control.
Since new applications are being actively sought, the short product cycle also requires rapid observation, analysis, evaluation, and reporting of safety risks. In many cases, we are faced with the following problems in fulfilling our customers' requirements
There are two indices for comparing battery performance: gravimetric energy density and volumetric energy density. Volumetric energy density is important when light weight and large energy is essential for a product, such as batteries used in smartphones. In the case of electric vehicles (EVs), where the battery must be contained in a given space and the weight of the vehicle is closely related to the driving range, the weight energy density is mainly important.
The required charge-discharge performance, cycle performance, and safety while storing as much energy as possible in a limited weight and volume require specialized scientific knowledge, material processing technology, and optimal facilities.
In order to solve the above issues, ENAX supports customers who wish to develop products by hearing their applications, sharing the issues, and providing support from electrode and battery element development to prototyping and mass production.
Specifically, research and development is conducted according to the following structure and process.
1. Proof-of-concept of next-generation batteries represented by all-solid-state batteries.
2. Performance verification and identification of production issues using battery cells of the same size as those used in products
3. Mass production process design and verification of processes and quality, establishment of QC (review of procedures and processes in assembly)
4. Responding to pre-production needs of several hundred to several tens of thousands of cells
5. Verification of pack assembly processes, impact of component changes and work safety
We support development from lab-scale proof-of-concept to pilot-scale testing and development for product demonstration. The pilot-scale demonstration includes safety and production process evaluations, as well as validation of the suitability and appropriateness of the product for transfer to mass production.
1. Requests and development requirements
First, we will ask you about your problems related to batteries and what you would like to achieve. ENAX will then define the specific battery development requirements to realize your product.
2. Material Search
Lithium-ion batteries use various materials such as positive (negative) electrode materials, conductive materials, electrolyte, and separators. We search for and select the most suitable materials according to development requirements.
3. Element Development
Element development is a phase in which the electrode recipe and electrolyte recipe are examined and then checked to see if they match the characteristics of the product according to development requirements. This is done in a single layer pouch cell, which is the smallest unit of a lithium-ion battery.
4. Functional verification
Verification is carried out in stacked cells that are close to the actual size for product mounting. For example, this phase evaluates the resistance, heat generation, durability, reliability, etc. when the input/output current required for the product is applied.
5. Verification of actual equipment installation
This is the phase in which we procure the necessary amount of dedicated materials based on the number of cells required for product mounting, and manufacture prototype cells in facilities and processes that are close to those used for mass production. In this phase, we verify whether the performance of the cells is as expected for use in the final product, and conduct tests to ensure compliance with regulations. This is also the phase to determine if the performance and quality are confirmed and can be transferred to small-scale production.
6. Small-scale production of products mounted on actual equipment
This is the phase that prepares for the transfer to mass production process. This phase mainly includes adjustment of manufacturing processes and lines using assembly facilities based on the assumption of mass production volume, adjustment of inspection contents and inspection processes to ensure mass production quality, and preparation of procedures, PL, QC, etc. for manufacturing.
7. Mass production transfer
The final phase is the transfer to mass production. Depending on the volume of mass production, ENAX not only handles mass production, but can also transfer production to a customer-designated manufacturing site.
1. Slurry making
Active materials, conductive materials, binders, and diluents (amphipolar solvents including water) that make up the electrode are made into slurry; ENAX verifies formulation recipes and fabrication processes, focusing on the dispersibility of the slurry that contribute to battery performance.
2. Coating
This is the process of coating the collector foil with slurry. ENAX has established a coating method that guarantees coating material properties* and minimizes variation by using comma reverse, comma direct, and slot die coating methods to achieve high quality coating. Unevenness or variation in slurry properties and coating methods not only causes defects in battery output and capacity characteristics, but also poses the risk of ignition. Electrode drying, an element of the coating process, not only directly affects battery performance, but also greatly affects production speed, and is therefore an important element of process development.
*Ensuring physical properties of the slurry = Establishing three elements: suppression of viscosity fluctuations, suppression of agglomeration, and stability of the coated surface.
3. Calendaring
This process is used to increase the mechanical strength of coated electrodes and at the same time adhere the active material to the current collector to improve electrical conduction. To ensure stable battery input/output, capacity, and cycle performance, cold and hot presses are used to achieve the designed electrode density and control in-plane variation.
4. Electrode slitting
ENAX's shear-cut type equipment enables processing of a wide range of sizes.
5. Battery cell assembly
A typical battery cell is manufactured under the following flow and environment
Related Articles
battery_cell-
battery_cell
-
battery_cell
-
battery_unit
-
media
Media Article on our development, "An Exterior Body for Lithium-ion Secondary Batteries" was published in the Nikkei (electronic edition) on October 25th and the Nikkei morning edition on October 26th (page 14).
(Reprinted with permission from Nikkei. Unauthorized reproduction/copying are prohibited © Nikkei) -
media
-
media
-
media
-
media
-
media
-
media
-
media