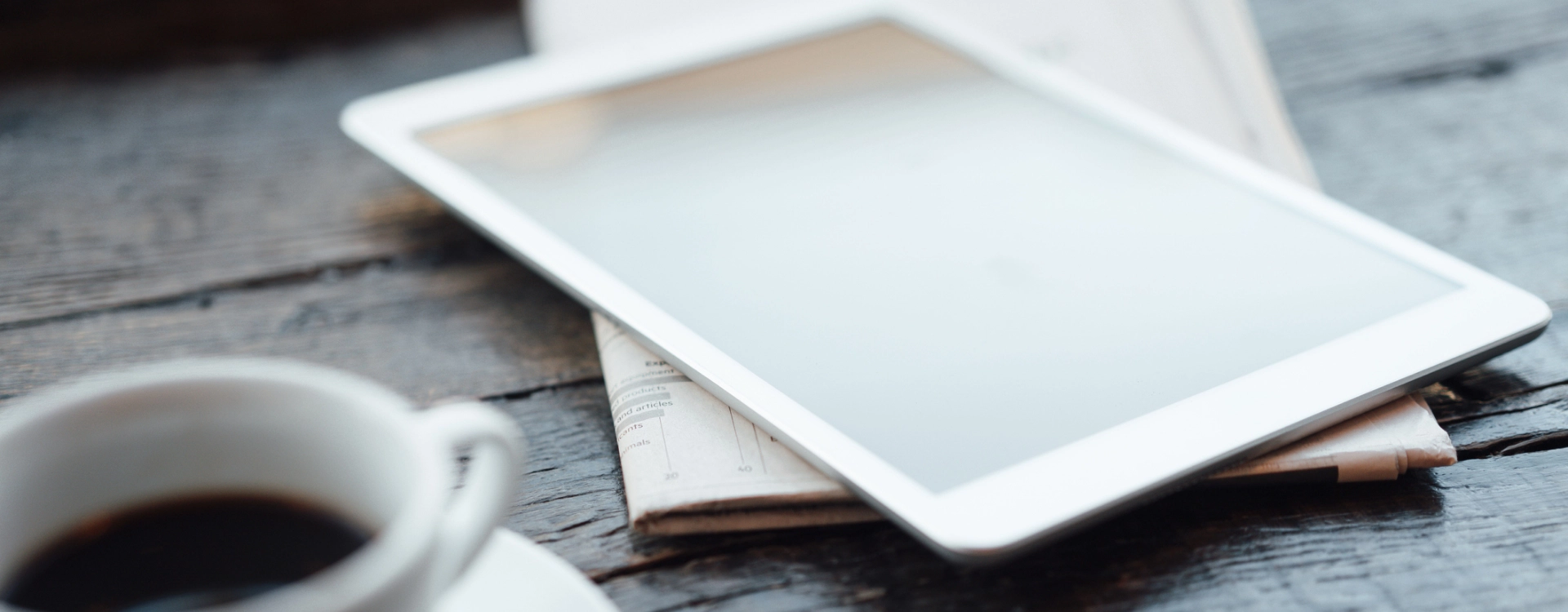
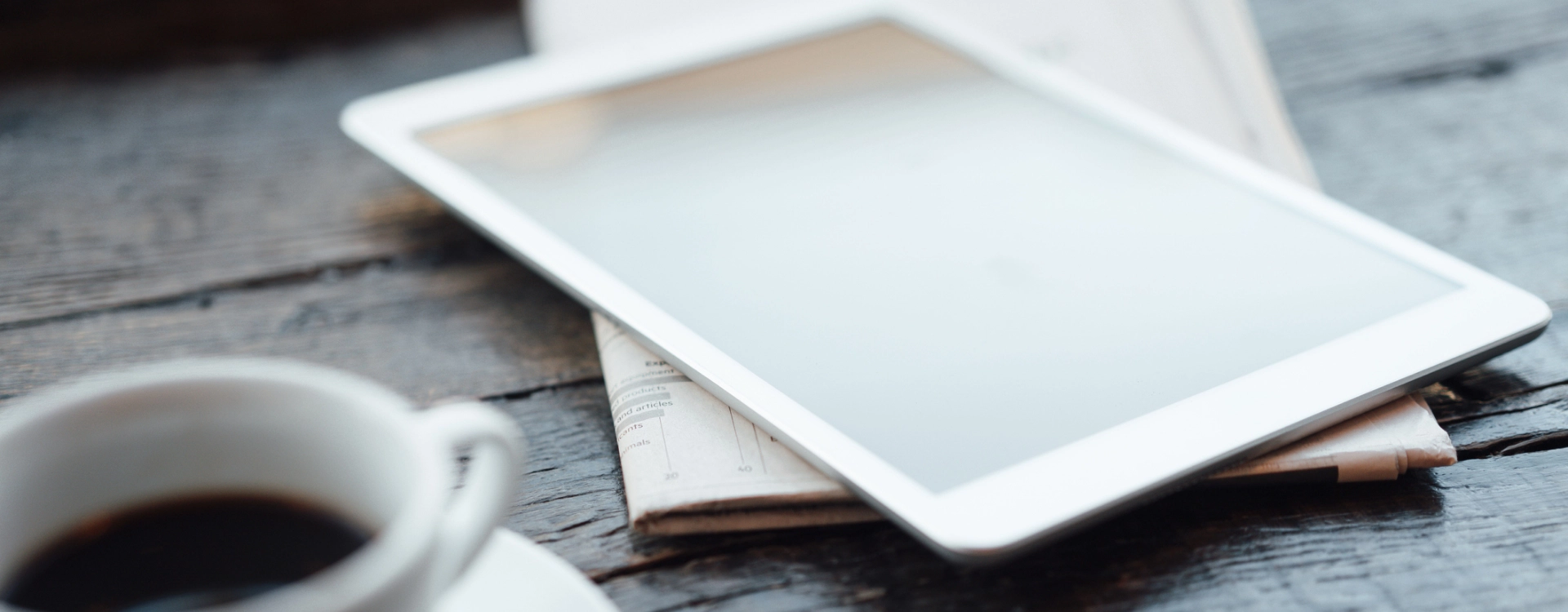
What is the battery enclosure development process that satisfies customer requirements and safety at the same time?
The need for rechargeable batteries that can be recharged and used repeatedly is increasing for the purpose of environmental friendliness, and ENAX has received many orders from major companies. This page introduces in detail the actual product development process, from the development of the housing to the final product as a battery pack unit.
Battery cells come in a wide range of performance and standards. To ensure that the required performance can be obtained for each application, ENAX offers a wide range of services, from selection and evaluation of battery cells to module design and structural design of the battery pack unit.
Particularly important in structural design is the first step, "planning". After hearing the customer's requirements and specifications, we make proposals to achieve both "target performance" and "suitable shape for the system". The optimal battery cell and housing shape varies depending on the materials used inside the battery, and delivery time and budget must also be taken into consideration.
At ENAX, we utilize our extensive know-how in battery development to determine how many battery cells to employ, what capacity and voltage settings, whether they can clear the specified current, and whether their life as a battery pack unit can meet our requirements.
Inquiries often come in when the size and shape of the space where the battery can be installed has already been determined. In such cases, we must design an individual housing that meets the space and shape constraints. In addition to achieving the specifications and performance required by the customer, ENAX, as a "battery professional," focuses on housing design and quality in the following points.
1. Busbar design and welding techniques to achieve the required current capacity
2. Thermal design to prevent battery heat retention and fire spread in the event of an abnormality
3. Pressure constrained design to maximize battery performance and life
4. Module fixing design to withstand mechanical vibration and shock of the product
5. Wire and FPC design for power and signal routing in localized and confined areas
In particular, thermal design and module fixation design are also important processes for safe use, and are evaluated by repeating various prototypes and tests.
In addition, many customers are surprised at the development costs involved in battery development, as many people have the image of "just replacing lead-acid batteries. If product development is carried out without sufficient consideration of quality requirements and design, rework may occur, and the time and development costs spent up to that point may be wasted.
To avoid such a situation, ENAX moves to mass production through the development process from principle prototyping to functional prototyping and pre-production prototyping.
ENAX listens to what customers want to realize from the planning stage, and makes economically rational proposals regardless of whether it is an existing product or a custom-made product.
For example, the battery cells that form the core of the battery pack unit are often made in China, Korea, Taiwan, or other foreign countries due to cost and ease of availability. Although people may have concerns about overseas products, we thoroughly control charging and discharging, check battery characteristics, and evaluate durability and life cycles to ensure safety.
Hazardous destructive tests, including nail penetration tests, are also conducted at our own factory. We can also take video of the tests and results and report them to our customers. In this way, we ensure safety both inside and outside the battery through the development of safety-conscious products.
ENAX has developed the battery pack unit based on the requests of many customers. For example, our laminated batteries, which are lightweight and have high energy density with a high degree of freedom in shape selection, have been used in industrial drones, AGVs, UGVs, and mobile robots as the highly reliable battery pack unit.
The above are just a few examples, but the following service pages contain various development examples that ENAX has worked on. We hope you will find it useful as a reference. The examples range from small battery pack units for drones, robots, and mobile devices to large capacity units for special vehicles and race cars.
Since lithium-ion batteries are items that are classified as "dangerous goods" during transportation, it is required to manufacture and evaluate products that meet international safety standards and import/export tests. ENAX can provide such safety certification.
We at ENAX are committed not only to developing safe battery pack units while meeting the requirements of our customers, but also to contributing to a sustainable world through our product creation assistance.
Please see "Example of battery pack unit development" for more information.
Related Articles
battery_unit-
battery_cell
-
battery_cell
-
battery_unit
-
media
Media Article on our development, "An Exterior Body for Lithium-ion Secondary Batteries" was published in the Nikkei (electronic edition) on October 25th and the Nikkei morning edition on October 26th (page 14).
(Reprinted with permission from Nikkei. Unauthorized reproduction/copying are prohibited © Nikkei) -
media
-
media
-
media
-
media
-
media
-
media
-
media